Project Description:
This is the third house in Massachusetts to achieve PHIUS+ Passive House Certification and the second one in Falmouth. The home, which is owned by the CPHC and his wife, has a living area of 2,400 ft2.
Building Type Summary:
Other Awards:
PHIUS+ Certified Project # 1096 April 2014
EPA WaterSense certified 2014
DOE Challenge Home Certified April 2014
Address:
Lat. / Long.:
Location Type:
Köppen Climate Type:
Climate Region:
Solar Insolation:
Annual HDD :
Annual CDD:
HDD Base Temp:
CDD Base Temp:
Occupancy Type and Details:
owner occupied
Conditioned Floor Area:
Conditioned Building Volume:
Semiconditioned Floor Area:
Unconditioned Floor Area:
Multiple buildings?:
Total number of units in project (all buildings):
Total floor area of project (all buildings):
Historic?:
Completion date:
Site description:
Flat lot, frontage is true South, 11,754 ft2
Materials:
Wood construction. Roofing was selected for Energy Star rating. Used paver blocks for driveway to minimize run off.
Energy Highlights:
Passive House PHIUS+ certified. House designed to face true South. 8.7 kw PV system, sized for house load plus future EV. Pre wired for garage EV electric car charger. Motorized exterior solar shade.
HERS Index:
Energy Star Score:
Annual renewable energy generated:
Electric Utility Company:
Gas Utility Company:
Datasets and Utility Bills sources and reliability:
source is utility bills and pv meter readings (for SREC program)
Electricity amount (imported from grid):
Electricity amount (credited or exported to grid):
Net electricity usage (purchased electricity):
Natural gas amount (purchased energy):
Energy Storage Capacity:
Energy Storage type:
house naturally stores heat energy in winter due to Passive House construction. No other storage devices are used.
CHP System Description:
NA
Subslab assembly:
10 inches of EPS, 6 mil poly sheet, 4 inch concrete, 1.5 inch EPS between sleeper studs. Total of 11.5 inches EPS. R values are for entire assembly from PHPP Model.
Slab edge assembly:
perimeter thermally isolated from stem wall with 4 inch EPS
Foundation wall assembly:
10 inch thick concrete stem wall
Above grade wall assembly:
2x6 16" o.c. outer wall, 4 inch space, 2x4 inner stud wall for a total insulated thickness of 14 inches. 4 inch closed cell foam on sheathing, and 10 inches dense pack dry cellulose. R values are for entire assembly from PHPP Model.
Flat attic assembly:
24 inches blown in cellulose between trusses. R values from PHPP Model.
Cathedral ceiling assembly:
NA
Door Area:
Space heating - Manufacturer & Model:
Space heating - capacity:
Space cooling - Manufacturer & Model:
Space cooling - capacity:
Domestic hot water - Manufacturer & Model:
Domestic hot water - capacity:
Domestic hot water - efficiency:
Ventilation - Manufacturer & Model:
Process:
Owner and occupant is a Certified Passive House Consultant (CPHC), who worked with the architect to design this Passive House. The CPHC worked with the PHIUS+ Rater and PHIUS to obtain PHIUS+ certification.
Design for Adaptability:
House was designed to minimize maintenance, water consumption, energy consumption, and chemicals. It was also designed using Age in Place methods for senior citizen living. Lawn is maintained using organic products.
Other Software tools:
Excel, PVWatt, Climate Consultant
Energy Modeling Software:
PHPP 2007
Outcome of project goals:
House has exceeded our expectations. Annual Consumption of electricity is 20%+ less than modeled
Discrepancies:
None. I found PHPP Model to be fairly accurate for energy usage, after correcting for latent cooling needs.
Total Cost of Project:
Construction hard cost:
Gross Cost of Renewable Energy System:
Value of Tax Credits for renewable energy systems:
Net Cost of renewable energy systems:
Federal incentives:
$10,400 for pv
State incentives:
$2,000 for pv
$7,000 for Mass Save Energy Star new construction
Annual Electric Savings:
Annual Revenue from SRECs or other renewable energy credits:
Advice:
Owning PV is preferable to leasing. Take full advantage of incentives (US Federal tax credit for PV, Mass Save Program, SREC program). Passive House construction premium pays for itself in reduced energy bills. Owners are essentially pre paying their energy bills.
Published References:
Fine Home Building Magazine 6 Issues 2014 and 2015. Publ # 240, 241, 242, 244, 245, & 249
Cape Cod Magazine October 2014
Special architectural measures:
Passive House design. Exterior Solar shade. Geothermal loop for pre heat and pre cool of ventilation air. PV Solar array sized for all household energy requirements plus future electric car.
Energy Strategies:
All electric house. No combustion in Passive House envelope.
Energy Use and Production Documentation:
Subslab R-value:
Slab edge R-value:
Foundation wall R-value:
Above grade wall R-value:
Flat attic R-value:
Average window U-factor:
Solar Heat Gain Coefficient:
Visible Light Transmittance:
Door U-Factor:
Cost per square foot of Conditioned Space:
Air Changes per hour, ACH50:
Project Photos:
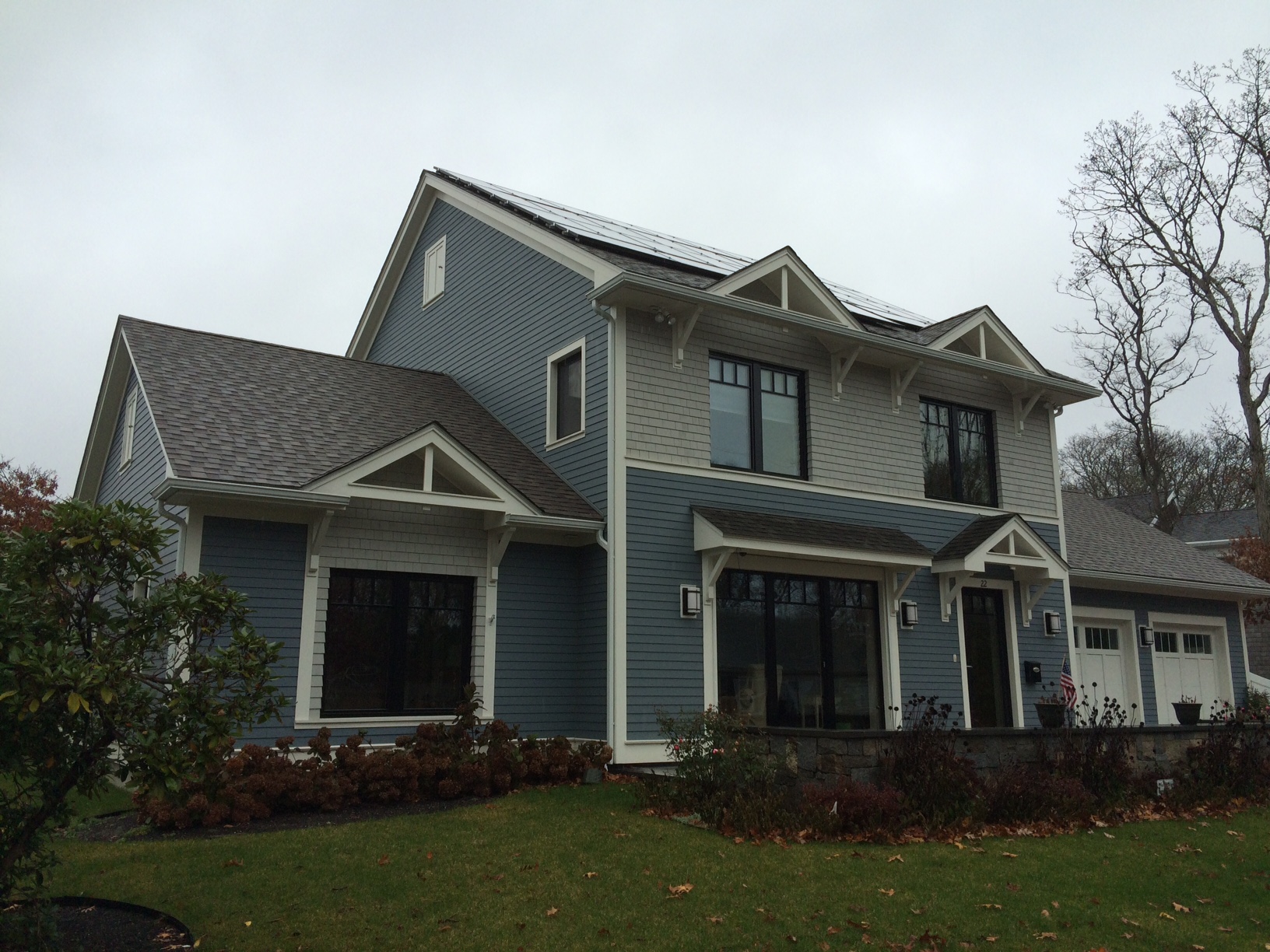
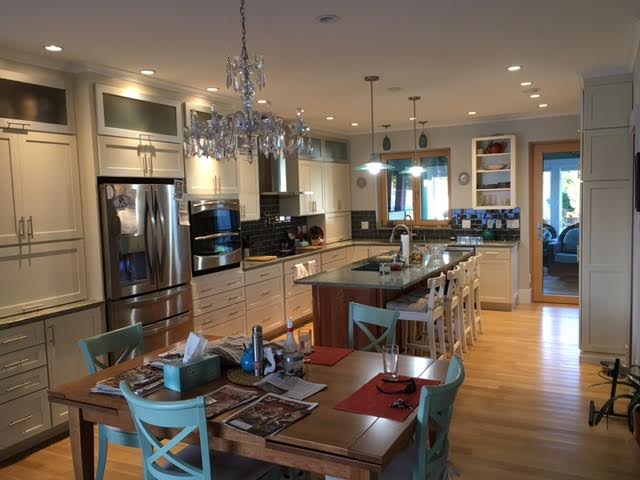
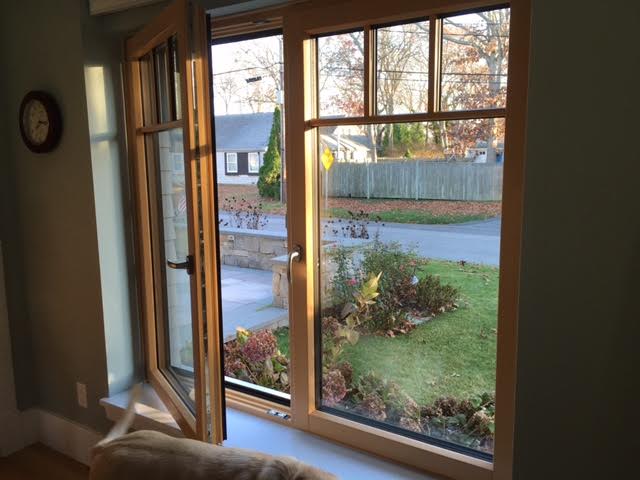
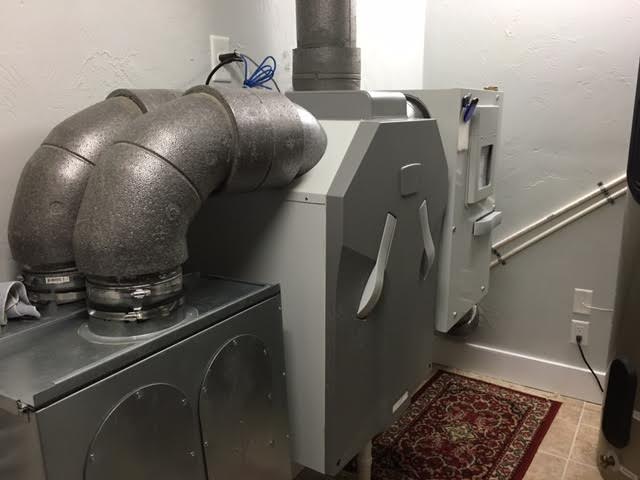
Number of Bathrooms:
Scope Description:
Total new construction of single family residence
Site conditions:
Renewable Energy Sources:
Other Purchased Fuels Description:
no
Storage Strategies & System Details:
NA
Summary of enclosure strategy/description:
Walls are double stud construction, 14 inch total insulated thickness
Window Description:
triple pane wood tilt turn windows with aluminum clad by Makrowin (Yaro). R values are for entire assembly from PHPP Model.
Door Description:
triple pane argon glass with wood frame aluminum clad, same construction as windows. R values are for entire assembly from PHPP Model.
Number of Bedrooms:
Project Team:
Team Member:
Team Member:
Team Members:
Steven Baczek, Architect
Dunhill Companies, Builder
Cotuit Solar, PV System
Mechanical Equipment Installation Details and Comments:
Each ventilation port was measured and set by a certified Zehnder commissioning expert